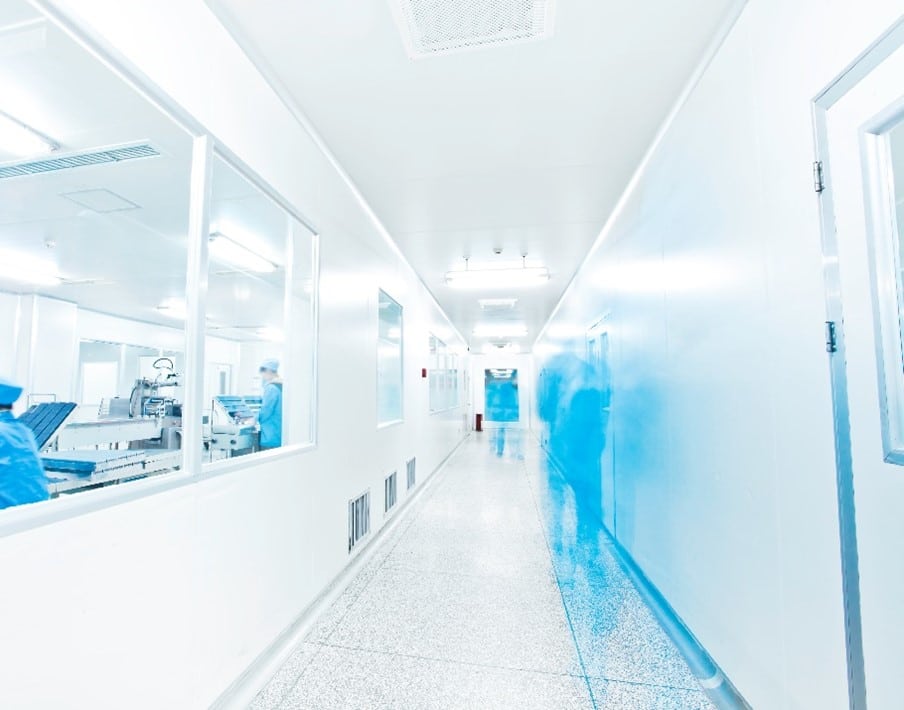
What are the air quality requirements for cleanrooms?
Cleanrooms are rooms where the concentration of airborne particles is controlled and kept at a very low level.
They are used by companies who need a very clean and sterile environment to manufacture or handle sensitive products, such as drugs, electronic chips, aerospace components, etc.
Cleanrooms help improve product quality, safety, reliability and regulatory compliance.
Cleanrooms are classified according to international standards, such as ISO 14644, which define the level of air cleanliness according to the number and size of particles allowed. Cleanroom classes range from 1 to 9, with 1 being the cleanest and 9 the least clean. Companies must choose the cleanroom class best suited to their business sector and purpose.
Contamination control in microelectronics rooms is essential to guarantee the quality of manufactured products, and to protect the environment and operators. Cleanrooms are used to minimize the concentration of airborne particles that can damage sensitive electronic products. They are controlled environments where temperature, humidity and pressure are regulated to minimize contamination. International standards are used to design a cleanroom and ensure that manufactured products meet quality requirements.
Photolithography, a set of techniques for transferring an image (usually displayed on a mask) to a substrate, requires this type of controlled environment.
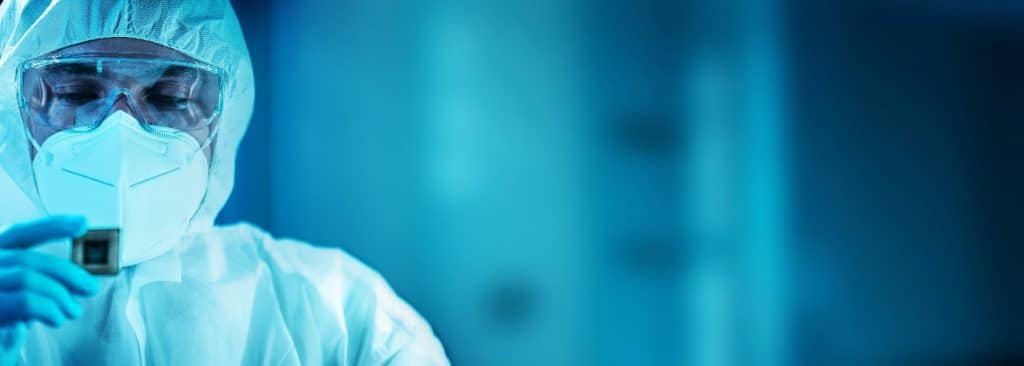
This technique is widely used in the semiconductor industry. Surface contamination can affect many of the subsequent steps in the photolithography process. Common issues are reduced adhesion and inclusion of defects. The key to eliminating these problems is to keep substrates as clean as possible.
How to control air contamination in cleanrooms?
It is necessary to control all supplies, liquids, machines, etc. that are newly incorporated into a cleanroom, as well as to carry out regular monitoring of cleanroom air quality.
TERA Environnement can support you in these 5 fields:
- Measuring chemical contamination in the air: Airborne Molecular Contamination (AMC)
- Measuring surface chemical contamination: Surface Molecular Contamination (SMC)
- Characterizing the outgassing potential of materials before introduction into cleanrooms
- Monitoring the shelf-life of molecular filters
- Searching for trace contaminants in deionized water EDI
Why choose TERA Environnement for your cleanroom contamination control?
Our laboratory has over 20 years’ experience in cleanroom contamination control, and boasts high-performance analytical equipment for the analysis of a wide range of organic and inorganic chemical contaminants present in air or on surfaces at trace levels.
Find out why you should choose our laboratory to help you control contamination in your cleanroom:
- Over 20 years’ experience in cleanroom air analysis
- High-performance analytical equipment for your analyses
- Wide range of compounds available for analysis
- Very low analytical thresholds or limits of quantification (LOQ) ranging from ppt to ppb
- Flexibility and responsiveness
Technical means for monitoring chemical contamination of air and surfaces in cleanrooms
The samplers to be used depend on the molecules targeted for analysis, the sampling environment and the thresholds to be reached (LQ).
It is recommended to take regular measurements of air quality in a cleanroom in order to have a reference state in the event of a “crisis”, and to be able to trace back more easily to the element contributing to the contamination problem.
Cleanroom air analyses are therefore carried out upstream of any contamination problem, during a crisis, but also downstream of a problem, in order to confirm the return to an acceptable level of contamination for the activities involved in the cleanroom.
TERA Environnement can provide you with the following samplers:
-
- Bubbler and bubbling solution
- Thermodesorption tube
- Filter
In some cases, the use of Radiello passive samplers or other active supports may be considered.
Compounds | Sampling method | Analytical method |
---|---|---|
Acids | bubbler and bubbling solution | IC |
Bases | bubbler and bubbling solution | IC |
Metals | bubbler and bubbling solution | ICP MS or ICP OES |
VOCs | thermodesorption tubes | ATD GC MS |
Condensables | thermodesorption tubes | ATD GC MS |
Crystalline silica | PVC filter | DRX |
TERA Environnement can provide you with the following samplers:
- Soaked wipes
- Wafer for characterizing compounds deposited on surfaces.
Compounds | Sampling method | Analytical method |
---|---|---|
Acids | swabbing with a wipe soaked in deionized water or leaching with deionized water | IC |
Bases | swabbing with a wipe soaked in deionized water or leaching with deionized water | CI |
Metals | swabbing with a wipe soaked in deionized water or leaching with deionized water | ICP MS or ICP OES |
VOCs | swabbing with a wipe soaked in an organic solvent or leaching with an organic solvent | GC MS |
Organophosphates | wafer exposure | (WOS) ATD GC MS |
Condensables | wafer exposure | (WOS) ATD GC MS |
As an alternative to wipes, whenever possible, deposits can also be sent directly to the laboratory for analysis. WOS ATD GC MS measurements are presented below, a state-of-the-art technique specifically designed to detect chemical contamination caused by low or non-volatile compounds (condensables and organophosphates) deposited on surfaces.
Specific WOS ATD GCMS analysis for "heavy" compounds
TERA Environnement has a WOS ATD GCMS for the analysis of condensables and organophosphorus compounds.
Measurements are taken on 6, 8 or 12 inch wafers (~ 15, ~ 20 or ~ 30 cm) previously exposed in a cleanroom for several days.
The wafers are then sent to the laboratory for degassing (WOS) and ATD GC MS analysis.
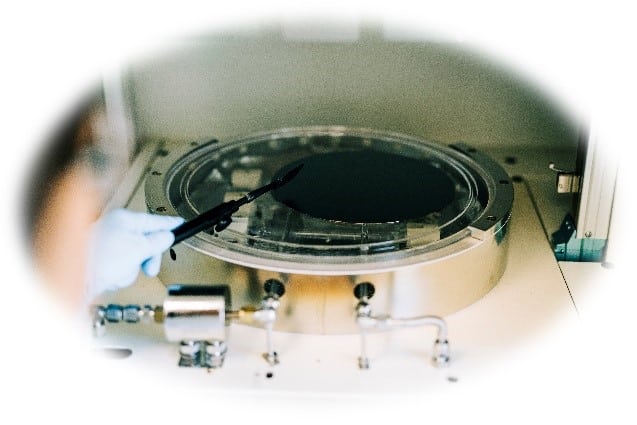
WOS: degassing of molecules present on the wafer surface and recovery of degassed compounds on a thermodesorption tube
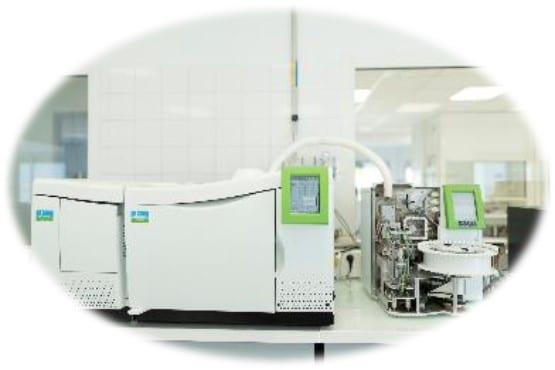
Thermodesorption tube analysis in ATD GC MS
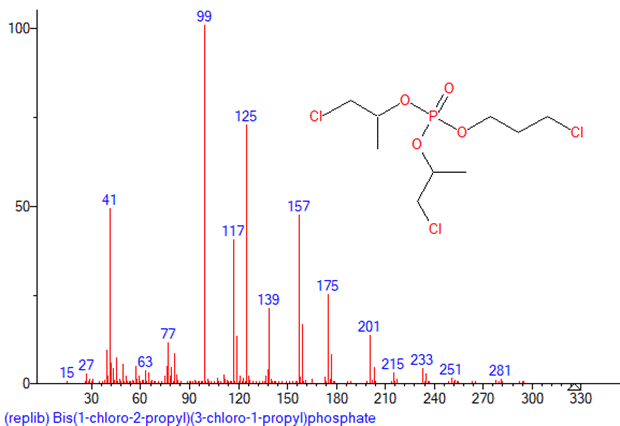
Mass spectrum of an organophosphorus
In terms of analysis, it is possible to carry out screening of the compounds present or to target specific ones.
Characterization of potential outgassing of µ-CTE materials
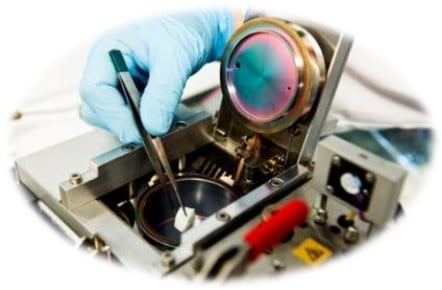
Before introducing new materials into the cleanroom, it is important to determine whether these materials can potentially emit compounds critical to cleanroom operations.
The material is placed inside the outgassing micro-chamber and swept by a stream of nitrogen (or air).
The appropriate sampler is placed at the µ-CTE microchamber outlet to target the molecules of interest (e.g. bubbler for acids or tubes for VOCs).
- Diameter: 6 cm
- Depth: 5 cm
- Air or Nitrogen flow
- Degassing temperature: 30°C to 250°.
Monitoring the service life of molecular filters
The filters used in cleanrooms filter both indoor and outdoor air, ensuring better control of air contamination in the cleanroom. Different filters are used, depending on the family of compounds to be filtered: acids, bases or VOCs.
The shelf life of filters can be determined by regularly measuring their level of contamination, and thus anticipating their replacement.
Compounds | Sample | Analytical method |
---|---|---|
Acids | Piece of filter extracted with deionized water | IC |
Bases | Piece of filter extracted with deionized water | IC |
VOCs | Piece of filter extracted with CS₂ | GC MS |
Trace contaminant detection in deionized water
TERA Environnement can test for acids, bases and metals at very low concentration levels in the ppt to ppb range in deionized water.
Compounds | Sample | Analytical method |
---|---|---|
Acids | Deionized water solution | IC |
Bases | Deionized water solution | IC |
Metals | Deionized water solution | ICP MS or ICP OES |
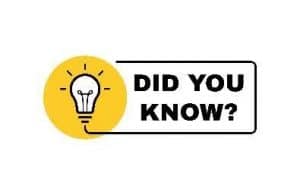
TERA Environnement has been helping its customers control chemical contamination in their cleanrooms for over 20 years!